Brazed Plate Heat Exchangers vs. Traditional Heat Exchangers: Which One is Right for You?
- Written by Viw Magazine
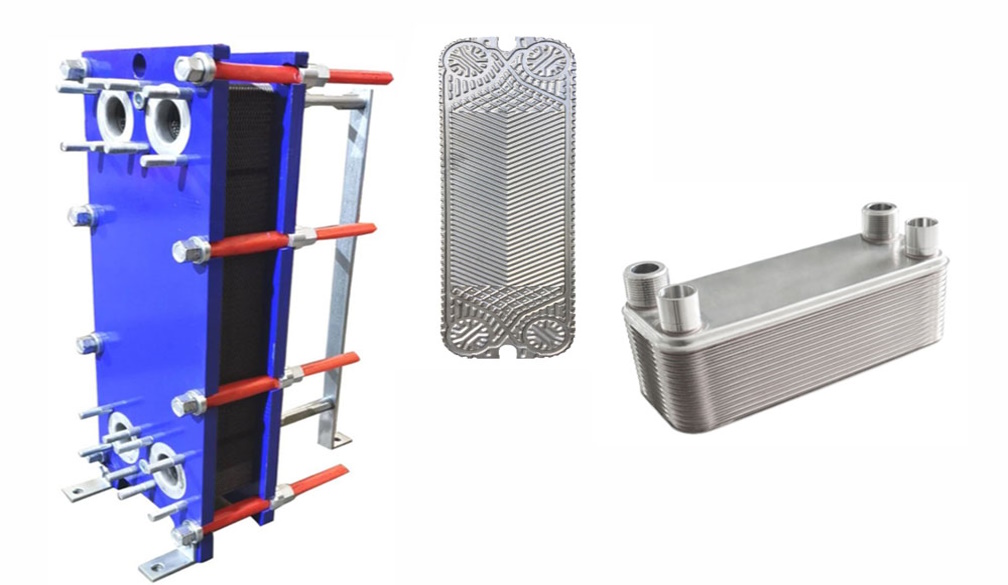
Whether it’s brewing, food processing, or industrial cooling, selecting the right plate heat exchangers can make all the difference in efficiency, cost, and maintenance.
Heat exchangers are vital in industries where precise temperature control is essential. Whether it’s brewing, food processing, or industrial cooling, selecting the right plate heat exchangers can make all the difference in efficiency, cost, and maintenance. But with various options available, how do you decide between a brazed plate heat exchanger and a traditional plate heat exchanger? Each type has its strengths, and choosing the right one depends on your industry, operational needs, and long-term maintenance considerations.
The Basics of Plate Heat Exchangers
A plate heat exchanger operates by transferring heat between two fluids without them mixing. This is achieved using thin, corrugated plates that create a large surface area for efficient heat transfer. These exchangers are widely used in brewing, food and beverage processing, and industrial cooling due to their compact size and superior performance. However, not all plate heat exchangers are created equal.
The two most common types are brazed plate heat exchangers and traditional gasketed plate heat exchangers. While they function on the same principle, their construction, maintenance requirements, and applications differ significantly.
Brazed Plate Heat Exchangers: Efficiency in a Compact Design
A brazed plate heat exchanger is a sealed unit where stainless steel plates are permanently fused together using copper or nickel brazing. This eliminates the need for gaskets and external framing, making it extremely compact, lightweight, and resistant to high pressures and temperatures.
One of the biggest advantages of a brazed plate heat exchanger is its high thermal efficiency. The brazing process allows for a more effective heat transfer surface, ensuring rapid temperature regulation. Because there are no gaskets, the risk of leaks is minimised, making this type of exchanger ideal for high-pressure applications.
Another key benefit is its low maintenance requirements. With no gaskets to replace or bolts to tighten, brazed plate heat exchangers require little upkeep, making them an excellent choice for closed-loop systems such as glycol cooling, brewery wort cooling, and industrial heating applications. However, since they are permanently sealed, they cannot be disassembled for deep cleaning, which can be a limitation in industries that require frequent sanitation.
Traditional Plate Heat Exchangers: Versatility and Easy Maintenance
Traditional plate heat exchangers consist of a series of stainless steel plates secured by a frame and gaskets. These gaskets create separate fluid channels while allowing the unit to be disassembled for maintenance and cleaning. This design is particularly beneficial in industries like food and beverage processing, where sanitation is a top priority.
One major advantage of traditional plate heat exchangers is their flexibility. Additional plates can be added to increase capacity as production demands grow, making them a scalable solution for expanding businesses. They are also easier to clean, as they can be opened and manually inspected to remove scale or residue buildup.
However, gasketed plate heat exchangers do require regular maintenance. Gaskets degrade over time, requiring periodic replacement to maintain efficiency and prevent leaks. Additionally, their larger size and frame structure mean they require more space compared to their brazed counterparts.
Which One is Right for Your Business?
The choice between a brazed plate heat exchanger and a traditional plate heat exchanger depends largely on your industry requirements and operational priorities. If you need a low-maintenance, high-efficiency unit for a closed-loop system with minimal risk of contamination, a brazed plate heat exchanger is a solid choice. Its compact size and robust design make it ideal for brewing, refrigeration, and heating applications where space and durability are key factors.
On the other hand, if you require easy access for cleaning, scalability, and long-term flexibility, a traditional plate heat exchanger is the better option. This is especially important for food and beverage processing, where sanitation and adaptability are critical.
For businesses looking for durability, high-quality stainless steel construction, and enhanced performance, investing in the right plate heat exchanger ensures efficiency, reliability, and cost-effectiveness in the long run. Understanding your specific needs will help you make the best decision for your operation.