How Custom Printed Fabrics Are Made: From Design to Production
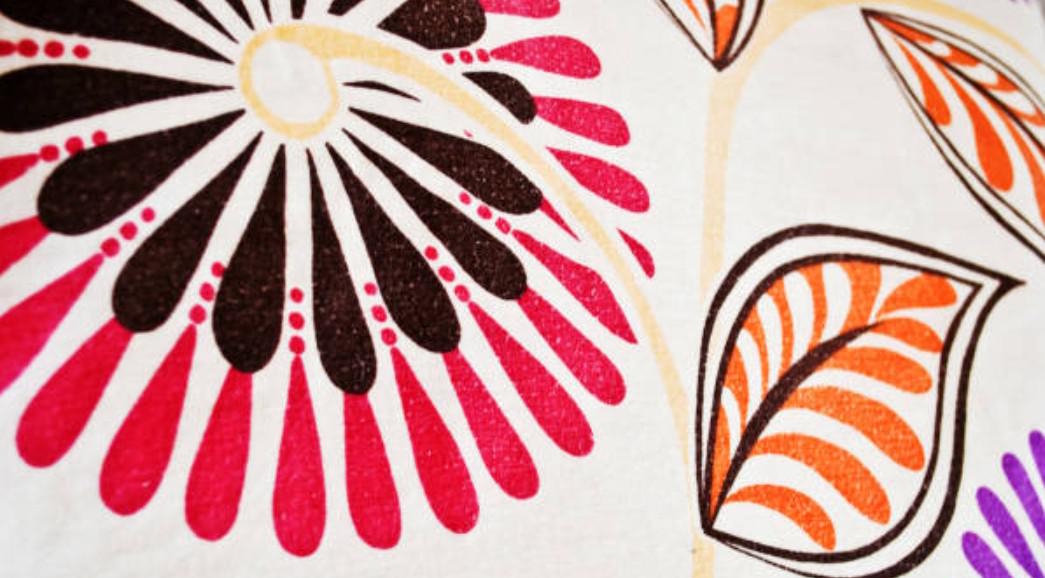
Individually printed fabric follows several phases prior to the final manufacturing stage. Digital designing is first step in starting this process. Designers manipulate colors, patterns and size using particular computer software. The finished design is transferred onto fabric employing multiple techniques of printing. Large-scale producing fits screen print the most well, while details best fit when doing digital prints. The ultimate result depends on the material used. Cotton, silk, polyester, and blended materials all respond differently to dyes. Fabrics are heat-set or steam-treated after printing to set the colors. Washing and finishing treatments enhance durability and texture. Quality control inspections guarantee that the colors are correct and the print is even. After approval, the fabric is cut and ready for use. Knowledge of the production process allows designers to create superior-quality custom fabric.
The Role of Thread Count in Custom Fabric Printing
Textured characteristics and printing clarity and durability of fabrics derive from their thread count measurement. The tissue contains threads arranged in a square inch pattern for measurement purposes. The number of threads per square inch determines how smooth the printed surface becomes so that details stay clear. The image sharpness depends on the roughness produced by lower thread count fabrics. Cotton fabrics exist in quantity ranges between 150 to 400 threads per square inch. The structures of silk and polyester differ but their operation functions in similar ways. When printing on dense fabrics the process may require special printing techniques because high thread counts provide better ink absorption. Weave patterns for textile materials as well as plain and satin kinds directly shape the consequences of printing. Loose fabrics enable ink to penetrate deeply but may cause details to blurry. The design clarity in custom printing fabric improves as the fabric weave becomes tighter but operators must be precise when applying ink. The selection of proper thread counts guarantees both excellent fabric performance along with maximum print quality.
How to Prepare Your Designs for Custom Fabric Printing
Quality custom printing fabric is assured by enough design preparation. Begin by deciding on the proper resolution for your design. Design images need a minimum of 300 DPI in order to contain detail well. Any less could cause the appearance of pixilation and a slightly fuzzy print. Print in the correct colour mode. RGB works fine for computer screens but CMYK will be your best bet for actual fabric printing. Prior to submission, make the design CMYK colour mode. Designing with consideration for the texture of the fabric. Distorting fine details by textured fabric. Noting intricate designs on coarse fabric. Smooth pattern for run-through designs. Repeating tile format minimizes misprint in printing. Test for colour contrast for readability on fabric. Printed colour may vary. Sample swatch checking can prevent errors. Consider margins and safe zones. Designs can slightly vary when printed. Reserve space near edges for cutting. Correct file formatting speeds up production. Save designs in TIFF or high quality PNG. A properly prepared design results in professional, richly coloured fabric prints.
How to Care for Custom Printed Fabrics to Prevent Fading
Proper care for custom printing fabric extends their lifespan because of correct maintenance procedures. Freely wash your print at all times when washing instructions exist. The prevention of fabric fading requires a combination of washing with cold water and mild detergent. Dyes age since their degradation occurs during exposure to strong chemicals. Turn the fabric pieces inside out before adding them to the washing machine. The printing surfaces stay intact because of reduced friction during proper maintenance. Strong stain remover along with bleach should never be used. The chemicals cause the fibres to break and colour to bleed. Duplex washing materials with hands results in less damage to printing elements. When using the delicate cycle, the user must apply it. A low speed spin setting protects fabric from harmful tensions. The different methods of fabric drying play a significant role in determining its operational lifespan.