5 Essential Types of Air Compressors for Professional and DIY Applications
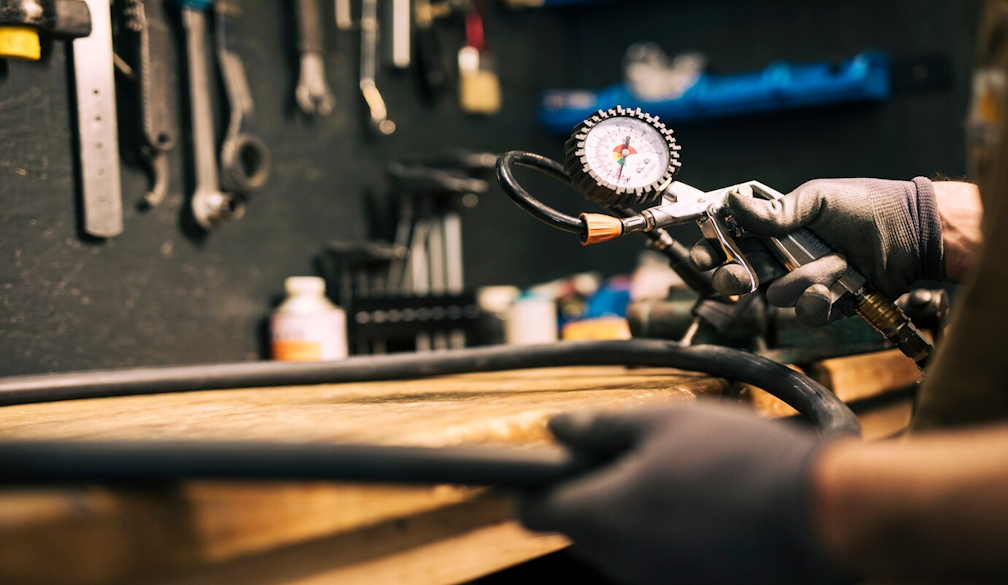
Air compressors serve as indispensable workhorses across numerous industries and workshops, converting power into potential energy stored as pressurized air. When selecting the right equipment for specific applications, understanding the functional differences between compressor types becomes crucial for optimal performance and longevity. Whether tackling industrial manufacturing or weekend DIY projects, the technical specifications and operational characteristics of each compressor type significantly impact efficiency and results. For professionals seeking reliable equipment, retailers like Autobarn offer comprehensive collections of best air compressors from Autobarn with varying specifications to match specific operational requirements. This article examines the five primary types of air compressors available today, analyzing their mechanisms, advantages, technical capabilities, and ideal applications.
Reciprocating Piston Compressors
Reciprocating piston compressors utilize a crankshaft-driven piston that moves within a cylinder to compress air. These compressors are classified into single-stage and two-stage variants, with the latter providing higher pressure capabilities through sequential compression chambers. Single-stage models typically deliver pressure ratings up to 150 PSI, while two-stage units can reach 175 PSI or higher.
The design employs intake and discharge valves that control airflow direction, with compression occurring as the piston creates a vacuum that draws air in, compresses it, and forces it into a storage tank. These compressors offer excellent pressure output for their size and provide good value for intermittent-use applications. However, they generate more heat and noise than other types, with operational sound levels typically ranging from 80-90 dB, and require regular maintenance due to their numerous moving parts.
Rotary Screw Compressors
Rotary screw compressors employ two interlocking helical screws to compress air continuously. As these screws rotate, the air volume between them decreases progressively, creating pressure. This technology allows for 100% duty cycles, making these compressors suitable for continuous operation in demanding industrial environments.
These systems typically offer CFM (Cubic Feet per Minute) ratings from 15 to over 500, with pressure capabilities between 125-175 PSI. Modern rotary screw compressors feature sophisticated microprocessor controls that monitor performance metrics and optimize efficiency, with many units achieving specific power consumption rates around 18-22 kW/100 CFM. Their sealed compression chambers require minimal maintenance while delivering oil-free air when specified, though their initial cost exceeds that of reciprocating models.
Centrifugal Compressors
Centrifugal compressors utilize high-speed impellers (typically operating at 20,000-75,000 RPM) to accelerate air radially, converting velocity energy into pressure energy. These dynamic compressors excel in applications requiring substantial airflow—often exceeding 1,000 CFM—while maintaining moderate pressure levels between 40-150 PSI.
Their oil-free operation makes them ideal for sensitive applications in pharmaceutical, food processing, and electronics manufacturing industries. With fewer moving parts than reciprocating models, centrifugal compressors offer exceptional reliability for large-scale operations. These sophisticated systems typically feature advanced surge control mechanisms and variable inlet guide vanes to maintain efficiency across different operational demands.
Scroll Compressors
Scroll compressors utilize two spiral-shaped scrolls—one fixed, one orbiting—to compress air through progressively smaller volumes. This orbital motion creates multiple compression pockets simultaneously, resulting in smooth, pulsation-free air delivery with minimal vibration.
These compressors typically operate at lower temperatures than reciprocating models and deliver oil-free air with pressure capabilities up to 145 PSI. Their compact design and quiet operation (often below 65 dB) make them particularly suitable for laboratory environments, dental applications, and other settings where noise sensitivity is paramount. Scroll compressors typically offer excellent energy efficiency with specific power consumption around 15-18 kW/100 CFM.
Rotary Vane Compressors
Rotary vane compressors employ a rotor with sliding vanes mounted eccentrically within a cylindrical housing. As the rotor turns, centrifugal force extends the vanes against the housing wall, creating compression chambers that decrease in volume as they rotate toward the discharge port.
These compressors deliver consistent airflow with minimal pulsation and operate efficiently at lower pressures (typically 100-150 PSI). They offer excellent reliability in dusty environments due to their simple construction and fewer moving parts compared to reciprocating designs. While they require regular vane replacement approximately every 9,000-15,000 operating hours, their lower initial cost and straightforward maintenance make them cost-effective for many commercial applications.