The Process of Metal Stamping and Forming
- Written by NewsServices.com
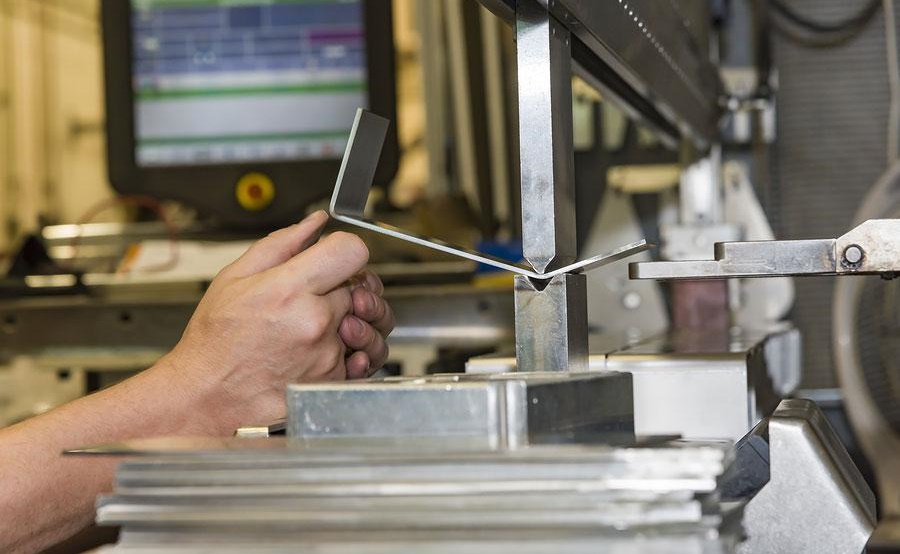
Many engineering processes take place in the machine shop, and one such complex process is that of metal stamping and forming. This involves the transformation of sheet metal into different shapes. In this process of material engineering, flat sheet metal pieces known as blanks are introduced into the stamping press, where a specialized tool works on it to provide the desired shape.
The procedure relies on pressure to work the sheet into the desired shape. The sections below discuss the different processes involved in metal stamping and forming in an engineering workshop.
Understanding the Concept of Metal Stamping and Forming
Metal stamping, also known as pressing, is often used in the low-cost manufacture of high volumes of identical parts. This material production method is employed by metal stamping services and is ideal for short and long-run operations and can run simultaneously with other metal forming procedures. Procedures that can be combined with stamping in the machine shop include
-
Flanging
-
Coining
-
Blanking
-
Embossing
-
Punching
-
Bending
Flanging involves the use of dies to introduce a flare or flange into the material piece. It is also common to make use of metal presses or other types of specialized tools.
Coining is a type of bending technique that involves engraving the workpiece between a die and a press. This enables the tip of the press to penetrate the material, thereby creating accurately designed imprints.
Blanking and punching are similar processes that involve using a die to cut the metal into regular pieces. In punching procedures, as the punch drives through the metal, the scrap material is left behind, leaving a hole in the metal. In the case of blanking, the workpiece removed from the primary material is the preferred component generally referred to as the blank.
The embossing process involves the creation of a raised or recessed prints in metal sheets. This is done by pressing the metal piece against the die with the pattern of the desired shape. This can also be perfected by passing the material through a roller die to achieve the desired print.
Bending is a general process involving forming metal into desired shapes such as U, V, and L depending on the desired profile.
Metal Stamping Machines
The machines used in the workshop for stamping procedures vary and depend mainly on the project's main aim. Based on the settings, they can do more than engraving, and other common operations include cutting, casting, punching, and shaping the sheets. There are equally machines that run on computer programs or those that make use of a computer numerically controlled (CNC) to offer high precision and repetition of prints on each stamped sheet. The use of computer-aided design (CAD) and electrical discharge machining (EDM) help ensure accuracy.
Different Metal Stamping Operations
In the machine shop, several processes take place in stamping operations, and they include
Progressive Die Stamping
This involves the use of different printing stations which are in sequences. This begins with the use of an iron coil introduced into a reciprocating stamping press with the use of a progressive stamping die. The press and the die move together, and when the die moves down, the die closes to stamp the press, forming the shape on the material. And when the stamp moves up, the material moves in a horizontal direction to the next station.
This movement must be precise as the material moves along while connected to the metal strip. On reaching the final station, the fabricated part is separated from the rest of the material. This process is ideal when you need to run a fabrication procedure for a long-run operation.
Transfer Die Stamping
This is similar to progressive die engraving; the only difference is that the material is separated earlier in the process. The transport between stations is made possible by using a mechanical system, usually a conveyor belt. This procedure is best for use on more significant parts that will need to be moved to other production process sections.
Fine Blanking
This procedure is best used for processes that require high accuracy and smooth edges. This process is usually carried out on a mechanical or hydraulic press or by a combination of both machines. Fine blanking involves using high-pressure techniques, and the machine operator must consider this when using this procedure.
Four-Slide Stamping
Also known as four-way or multi-slide stamping, and is best used for manufacturing complex parts with numerous twists and bends. Instead of a single vertical slide, it utilizes four sliding tools to shape the material through multiple deformations. This process uses no dies; instead, two rams or slides strike the material horizontally to achieve the desired shape. It is a relatively low-cost method of production and is best for high-volume manufacturing.
Different Types of Stamping Press
When it comes to the machine shop, there are different types of presses used to mark and create shapes onto the workpiece. The common engraving press you’d find here include
Mechanical Press
Here a motor and a flywheel are connected to transfer and store energy. The punches are of various sizes ranging from 5mm to 500mm, and this depends mainly on the press in use. Some options strike up to 1,500 strokes per minute in terms of speed, with the minimum starting from 20. While there are low-weight presses available beginning at 20 tons, heavier ones usually run into the range of 6,000 tons. You can find more here on the anatomy of a mechanical press.
Hydraulic Press
In a hydraulic press, a pressurized hydraulic fluid is used to apply force to the material. The fluid is displaced with the help of hydraulic pistons, and the exerting force is proportional to the piston’s head diameter. This makes it easy to control the amount of pressure and which is more consistent than the mechanical press.
Final Note
Metal engraving and forming is an essential aspect of engineering manufacture and is critically used in the machine shop to create desired shapes and imprints on a material piece. The engineer uses different tools to ensure precision and make sure the process is safe and reliable.