The 7-Step for Shell Mould Casting Process
- Written by NewsServices.com
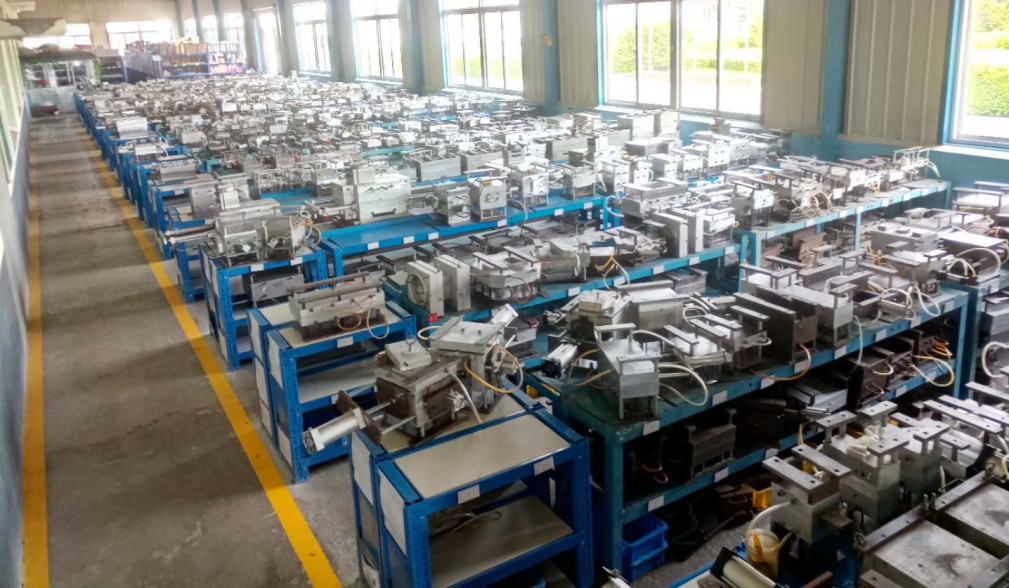
Shell moulding can be used for various small scale productions, ranging from automotive applications to intricate jewellery pieces. Since the beginning of mass production after WWII, it has been used extensively in virtually all major industries. Recently its importance has also strongly come to the fore again within the field of artistic reproduction processes for objects with high value to weight ratio, especially when making limited editions or one-off pieces. Some of the major and biggest steel casting industries are also using the same approach, dawangcasting.com is also one of them.
Pattern used in shell moulding is normally made up of two matching pieces. One is the core and the other is the shell. While cores can be made of metal or plastic, shells are normally moulds made from polymer clay (such as air-drying modelling clay), often in combination with a release agent such as talcum powder/liquid soap mixture to allow easy removal after firing. In some cases, moulds are made from rubber or silicone moulding compounds.The process of shell mould casting is relatively easy and can be done at home. It involves pouring metal into a mould that has been created using 2 halves of a mould with the pattern for the piece between them. The pattern makes up one half of the mould and wood, or something durable, will make up the other half of the mould. The following steps will guide you through the process of shell mould casting:
- Create the Pattern
The first step is to create the pattern for the piece that you want to cast. This can be done using wood, or another material that is durable and can withstand heat. The pattern must be precise in order to ensure a good fit between the 2 halves of the mould. If you are creating a piece using clay, it is best to fire the clay before making the pattern as it will be less likely to deform and change shape when heated later on.
If your pattern is made from wood or another material that cannot stand high temperatures it should be covered in something like wet cloths which can help protect against heat damage. Then line the inside of both halves of your mould with this same cloth (or other material) as this will prevent any metal seeping through due to temperature variation between your two halves.- Mark Your Mould
Once you have created your pattern, place it inside one half of your mould and make sure it fits properly before marking where its outline is on the outside of your mould wall. You can do this using nails or another form of marker.
- Prepare Your Mould Area
Once you have marked where your pattern is placed in your mould, prepare your mould area by covering it with aluminium foil and adding a layer of sand to the top of it. Make sure that everything has been covered properly so that there are no gaps before moving onto the next step as any metal seeping through these gaps will be lost and reduce the amount available for you to use.
- Preparing Your Wood Pattern
Your wood pattern needs to be prepared before you fill it with metal as doing so afterwards may result in damage due to expansion from heating the metal up too quickly within a confined space. One way to do this is to drill a hole in the pattern and then fill it with charcoal. This will help to evenly heat the metal and stop it from expanding too quickly.
- Pour Your Metal
Once your mould area is ready, carefully pour your metal into the top half of the mould. Make sure that you pour it slowly and steadily to avoid any turbulence which could cause the metal to seep out of the mould.
- Allow the Metal to Cool
Once you have poured your metal, allow it to cool completely before removing your finished piece from the mould. If you try to remove it while it is still hot, you may damage your final product or even injure yourself.
- Clean Up
Once you have removed your finished product from the mold, it is time to clean up. Make sure that you dispose of all the sand and aluminium foil properly and that everything is tidy before moving on to the next project.
Advantages of shell moulding:
- * It is a cheap process with only a few tools required. It's quick, easy and can be done at home.
- * The final product has a smooth surface.
- * The final product is hollow.
Disadvantages of shell moulding:
- * It is a slow process.
- * The final product is not as strong as products made through other casting processes.
- * There is a higher chance of defects occurring with shell moulded products.
- * The finished product may have a rough surface.
Conclusion:
Shell mould casting is an easy to do at home process that works well for creating lighter weight, hollow metal products that cannot be produced using other casting processes. The main disadvantage of the process is that it takes longer than other processes and there is a higher chance of defects occurring, however this doesn't need to stop you from giving the process a go. With a bit of practice, you can create beautiful and sturdy products using shell moulding. To read more about shell moulding, we would suggest you visit Wikipedia or engineer world.